‘Remaining Tough Under Pressure’ – Support Surface Covers in the Post-Pandemic World
(-EUR ING Dave NewtonA,C,D, M.Eng, C.Eng, MIET, MIEEE, Richard HaxbyB,C,D, BSc (Hons) Ebor)
Support surface contamination via ingress through the cover material has long been a concern.
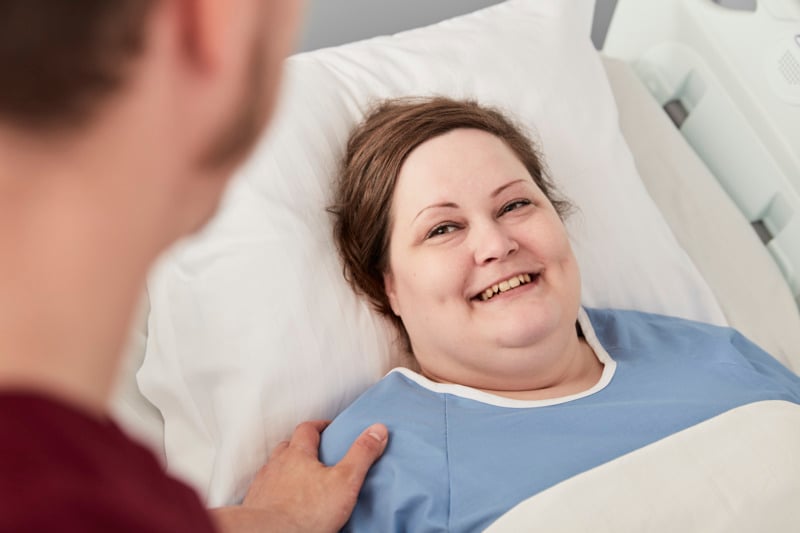
Background
Support surface contamination via ingress through the cover material has long been a concern1,2. The cover has been acknowledged as a potential area of patient risk due to cross infection but also can form a very visible and identifiable failure mode of support surfaces within healthcare facilities.
The COVID-19 pandemic resulted in a dramatic shift in the cleaning/disinfection processes of medical products generally and this was seen specifically with the specialist coated fabrics used on support surface covers. There has been an understandable move by both equipment rental companies and healthcare facilities towards the use of stronger and more aggressive cleaning agents as well as using longer cleaning chemical contact times.
The pandemic therefore demonstrated a clear need for even more robust and resilient cover fabrics that can continue to provide the critical performance parameters needed by support surfaces over a long period of clinical use. The use of impaired and damaged covers in clinical practice can add unnecessary risks relating to infection, potential patient harm and potential legal negligence.
The cover of a support surface is critical as it forms the interface with the patient’s body and if compromised can be a potential source of infection to the patient. A support surface has to handle a range of different sources of wear and tear and still remain both safe and effective through maintaining features such as microclimate management and protection from liquid ingress (Figure 1). Polyurethane-coated fabrics are often preferable for support surfaces as they allow moisture vapor to diffuse through the cover, moving moisture away from the patient skin and working in conjunction with other moisture-handling systems within the support surface. The cover fabric is also there to protect the support surface core, acting not only as a barrier to fluid ingress but also as a barrier to bacteria and viruses that may be present on the mattress surface between disinfection activities.
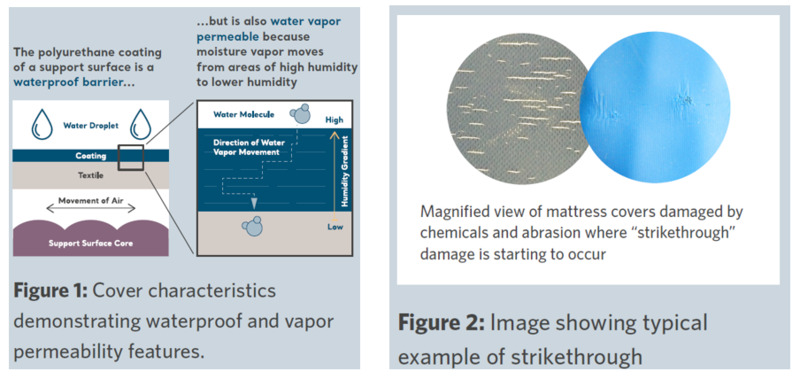
As well as the effect of constant patient use and cleaning – the cover also has to remain resilient to the effects of equipment handling and medical equipment placed on the bed that can potentially result in physical damage resulting in a failure of the waterproof nature of the cover.
Covers also need to be resistant to damage from abrasion (from manual handling and in-use), resistant to tearing (for example due to damage from X-ray cassettes) and resistant to damage from the aggressive cleaning agents now widely used in hospitals to kill pathogens.
The combination of chemical attack from cleaning materials and physical damage due to ancillary devices located in the patient area can directly affect product life through damage to the top cover of the material. Support surfaces go through rigorous cleaning and disinfecting routines, typically with the use of harsh chemicals. Such actions can cause damage such as microscopic tears and cracks in the fabric cover, commonly known as strikethrough damage that is not easily seen with the naked eye. This can compromise the cover over time and allow for the seeping of bodily fluids and other hazardous substances into the support surface.
New industry-developed tests are becoming available that can be used to demonstrate continued cover integrity and performance after this enhanced cleaning and disinfection.
Methodology
The ISO mattress standards group (TC173/WG11) has recently published a new method for determining the durability of mattress fabrics to cleaning agents – ISO20342-53. This is intentionally a very aggressive test, challenging the fabrics with continuous exposure to a cleaning agent. After exposure, the fabrics are tested to see that they are still waterproof; still maintaining the barrier to bacterial contamination. Fabrics are tested in cycles of 24-hour exposure, with many general-purpose materials expected to fail after only one or two cycles of this stringent test.
Testing to ISO20342 Part 5:2024 was used as a durability test for resistance to cleaning/ disinfection on two different polyurethane (PU) materials that are widely used for support surface covers (Figure 3).4,5
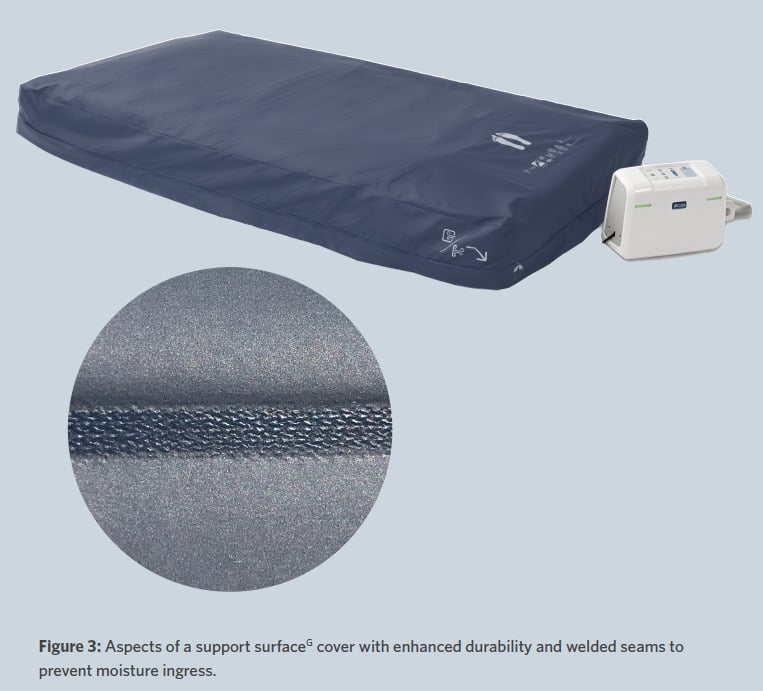
A standard materialE and an enhanced durability materialF were evaluated to demonstrate the effectiveness of the cover materials and the differences between the standard and the enhanced durability version using this new industry-developed test method. Three different types of cleaning chemicals were used in the study.
The test involves cycles of 24 hours of constant soaking of the test fabric with the test chemical, resulting in a 24 liquid contact time. The test chemical is typically used for disinfection during manual wipe-down cleaning.
A performance test of the fabric moisture barrier is then undertaken, using an industry-standard ‘hydrostatic head’ pressure test at 20 kPa (which is equivalent pressure to being 2 m/>6 ft underwater), and any leakage through the material is deemed a failure. This test pressure is well in excess of the pressure that would be exerted by the moisture present on a support surface but allows early indication of potential liquid paths though the PU cover material that could form a breach of the fluid-proof, virus-proof barrier that is so important for infection control.
Failure is fully anticipated as a result of the intentionally challenging nature of the test method, it is specifically constructed to allow comparison of how many cycles can be survived.
This newly published method is entitled, ‘Assistive products for tissue integrity when lying down – Part 5: Test method for resistance to cleaning and disinfection’3. It was developed as a global test method as part of ISO20342:2022, using expertise from a wide range of industry and healthcare contributors. This test method is being further codified into a European harmonized standard within the wider EN20342 standard with the aim of spreading industry-wide best practice and consensus on the need to improving the ability of support surfaces to withstand the new paradigm in cleaning practices now widespread.
Results
The results are shown in Figure 4 for bleach-based cleansing materials, Figure 5 for chlorine-based cleansing materials and Figure 6 for quat-based cleansing materials.
The results are shown graphically in terms of the number of cycles (each with an individual 24-hour contact time) before the failure of the waterproof barrier characteristics of the fabric.

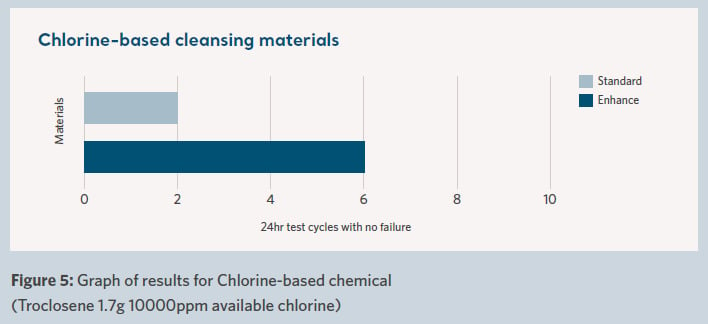
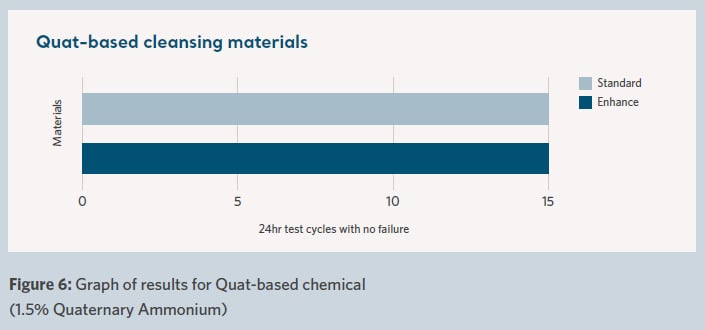
Discussion
The difference in performance between the standard and enhanced durability fabrics can be clearly seen. This is notable between the two materials for each of the three different chemicals tested.
Each cycle of 24-hour exposure provides an intentionally accelerated test compared to that experienced with a normal manual wiping protocol of chemical application, rinsing, and drying. The continuous contact between the cleaning agent and the cover is intended to maximize chemical interaction causing the reaction and degradation to occur much faster and more aggressively than would be seen within practice when using the recommended cleaning and disinfecting procedures.
The test method has been developed in conjunction with fabric manufacturers to specifically demonstrate differences between fabrics in response to cleaning chemicals through the principle of accelerated failure. The use of accelerated test methods is well established in industry and this approach allows the cumulative effect of years of typical use to be achieved in a much shorter test timeline.
The chemical reaction effect of the liquid contact during the entire 24-hour contact period is many times that of the normal cumulative effect of normal cleaning. For example – if a typical manual cleaning cycle in a hospital involved a 5-minute disinfectant contact time, one test cycle of 24 hours is mathematically equivalent in chemical attack terms to approximately 266 individual daily manual cleaning cycles. However, in practice, the 24-hour contact time may have a much more aggressive effect than the cumulative time would suggest – each cycle is therefore equivalent to years of manual cleaning.
This study was undertaken to show the differences and effectiveness of these materials for use for support surface covers where they need to continue to provide necessary material functionality even after extensive levels of cleaning/disinfection. The cleaning chemicals are consistent with those being used routinely in hospitals since the pandemic.
The authors are contributing members of the global initiative around the IS020342 technical committee that is developing a range of global test standards and recommendations for assistive products intended for issue integrity (APTI’s) – a generic term that includes support surfaces.
This work includes the released test method detailed as Part 5 of the ISO standard which was used for the results shown in Figures 4, 5, and 6. The authors are also part of the NPIAP/S3I team that created the NPIAP’s cleaning guidance for support surface covers that communicated accepted best practices. This work is presented as part of the promotion of wider education regarding the standard and this cleaning guidance.
It is important that manufacturers, equipment rental companies, healthcare facilities, users and providers of cleaning materials/services have an effective and consistent test method that can be used to assess the compatibility and effectiveness of the cover and cleaning processes. This test specifies a globally accepted method to evaluate the effects of liquid cleaners and disinfectants on the properties of waterproof coated textiles that are used as the protective outer surface of assistive products such as support surfaces.
In clinical use, it is NOT recommended to leave chemicals permanently on the cover material after the required cleaning contact time – chemicals should always be removed via rinsing with water using a dampened cloth. If allowed to dry without rinsing, the chemical residue can form a hazard to the patient skin. It is important to follow the manufacturer’s instructions for both support surfaces and cleaning agents.
It is clear from the test results that cover material failure may still occur within a facility, particularly if the manufacturer’s instructions have not been followed. However, with an enhanced cover material a much longer duration of misuse is expected before leading to a failure. It is essential that within facilities a vigilant approach is taken to ensure there is a regular inspection of the cover in compliance with the manufacturer’s recommended inspection instruction.
The ‘4 way’ stretch characteristics of a support surface top cover is particularly important during patient loading as the cover material is deformed in a 3-dimensional manner to allow pressure redistribution via immersion and envelopment. This is even more important for active surfaces, for example using those using alternating therapy modes. The regularly changing surface characteristic can provide enhanced pressure redistribution but also results in the fabric being repeatedly stretched as the active surface cycles. The improved chemical resistance ensures that the ‘4 way’ stretch characteristics of the support surface cover material remain consistent due to the reduced impact of chemicals on the polyurethane. This is vital to ensure consistent product performance over the product lifetime providing consistent pressure redistribution, immersion, and envelopment.
Selecting the right cover fabric for your support surface can be challenging. Many fabrics may look the same, but can be coated with a wide range of polymers with very different physical properties - including enhanced durability. Using materials with enhanced chemical resistance can lead to reduced risk of hospital acquired infections and legal risks associated with patient harm, improved product lifetimes, reduced warranty claims, and an improved ability for installed equipment to adapt to changing cleaning regimes.
Conclusion
The cover material is a key element in the design and construction of a support surface. It is important in ensuring both patient safety and the optimum therapeutic operation.
It is essential that within facilities a vigilant approach is taken to ensure there is a regular inspection of the cover in compliance with the manufacturer’s recommended inspection instruction and that recommended cleaning instructions are followed.
This study demonstrates that the cover material selection can be based on a recognized international standard that can easily evaluate robustness to cleaning. Having a more chemically durable and hence longer lasting cover material that still fulfils the intended design requirements is vital in protecting the patient and the important investment in procurement and training associated with the selected support surface.
Download the Support Surface Cover Fabrics Brochure
Get personalized advice and solutions. Talk to an expert today!
References
- How Wet Is Your Patient’s Bed? Blood, Urine, and Microbiological Contamination of Mattresses and Mattress Covers | Pennsylvania Patient
- Safety Authority Advisory 2018.
- Best Practices for Cleansing, Disinfecting, and Care of Polyurethane Support Surface Covers, S3I guideline, NPIAP.com
- ISO/DIS 20342-5 Assistive products for tissue integrity when lying down — Part 5: Test, method for resistance to cleaning and disinfection
- Premium Support Surface Covers, A00131.3.0.INT.EN, www.arjo.com
- Technical Data Sheet END464, Trelleborg Engineered Coated Fabrics, February 2019, trelleborg.com
Acknowledgments
- Advanced Development Manager, Arjo Inc, USA
- Technical Director, Trelleborg Engineered Coated Fabrics, UK
- ISO20342 Committee member
- NPIAP/S3I Committee member
- Material tested was Arjo Reliant IS2 material, supplied by Trelleborg ref: PER464
- Material tested was Arjo Reliant Premium, supplied by Trelleborg ref: END464.
- Arjo Covers Trelleborg NPIAP Cleaning Guidance ISO20342-5 G: Auralis is an example support surface available using Reliant Premium material